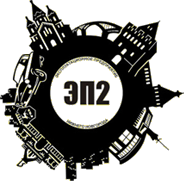
- Наружное утепление стен
- Фасадные работы
- Ремонт рустов
- Ремонт температурных швов
- Кровельные работы
- Ремонт дымоходов
- Промышленный альпинизм
- Ремонт входных групп
- Капитальный и косметический ремонт подъездов
- Ремонт ГВС ХВС
- Площадки для ТБО
- Металлоконструкции
- Уборка снега
- Полезная информация
- Благотворительность
- Отзывы
Виды газобетонных блоков, характеристики, а также плюсы и минусы. Как газобетон делают
Газобетонные блоки — практически идеальный строительный материал
Газобетонные стеновые блоки представляют собой изделия, сделанные из ячеистого бетона. Из чего же состоит газобетонный блок? Для его изготовления берется кварцевый песок, вода и цемент, присутствуют дополнительные компоненты. Блоки делаются в специальных печах, где обеспечено высокое давление и температура.
Что такое газобетон
Этот материал легкий и прочный, но обладает отличными свойствами, в том числе, плотностью и прочностью, теплопроводностью. Многие строители считаются газобетонные блоки идеальными, когда речь идет о строительстве до четырех этажей. Они отлично подходят при возведении стен и перегородок, в монолитном строительстве блоками этой категории можно заполнять проемы.
Газобетон был изобретен давно, но с разработкой новых современных производственных технологий, стали выпускаться усовершенствованные газобетонные блоки различных конструкций и видов.
Состав газобетонных блоков
Производятся современные газобетонные блоки из песка и извести, цемента, алюминиевой пудры. Токсичных веществ готовый материал не выделяет, поэтому по характеристикам его часто сравнивают с деревом.
При том, что блоки имеют дополнительные плюсы – не гниют и не подвержены естественному процессу старения. Материалы, которые входят в состав блоков, экологически чистые. Радиационный фон готового изделия не превышает 11 мкр/ч.
Благодаря простому составу блоки получаются пористыми, поэтому строение будет постоянно дышать пропускать воздух в помещение, от чего находиться в нем будет приятно и комфортно.
Из чего делают газобетонные блоки:
- Смеси цемента и извести;
- Кварцевого песка;
- Алюминиевой пудры;
- Воды;
- В зависимости от особенностей производства могут добавлять смеси, улучшающие свойства газобетона.
Газобетон представляет собой пористый строительный материал, который, чаще всего, прессуется в виде блоков. Главным компонентом для производства является цемент в сочетание с известью, также песок.
Пенобетон и газобетон: существенные отличия
Часто газобетон сравнивают с пенобетоном, более того, эти материалы могу путать. На самом деле они сильно отличаются друг от друга по компонентам, способу производства и основным характеристикам.
Пенобетон — это более дешевый материал, при производстве которого вместо кварцевого песка используются производственные отходы. Пенобетон дозревает на воздухе, а это значит, у него более низкие эксплуатационные качества.
Блоки газобетона будут иметь коэффициент теплопередачи гораздо выше. Поэтому уровень теплоизоляции в готовом строение также будет выше. В среднем при толщине стен от 400 мм от уже будет равен принятым средним показателям.
Газобетон не дает усадку в процессе эксплуатации, а вот от пенобетона усадки надо ожидать. Из всего сказанного становится понятным, почему пенобетон дешевле описываемого материала на 20-25%. Но при покупке более дешевого материала также возрастает риск купить некачественный пенобетон, который в итоге придется заменять более надежными материалами.
В пенобетоне поры распределены не равномерно, они также отличаются по размеру. Также более углубленное внешнее изучение материалов показывает, что первый практически не имеет отклонений в геометрии, а во втором случае такие отклонения могут достигать 10 мм.
Отличать также можно по внешнему виду. Газобетонные блоки по цвету всегда белые, а вот пенобетон более темный и серый. Если разрезать первый вид блока, то будет видна упорядоченная пористая структура и каждая ячейка в точности повторяет другую.
На основании этого можно сделать вывод, что газоблоки все же лучше, чем пеноблоки, хотя и существенно дороже, но за качество всегда приходится платить больше.
На фото идеальная кладка из газобетонных блоков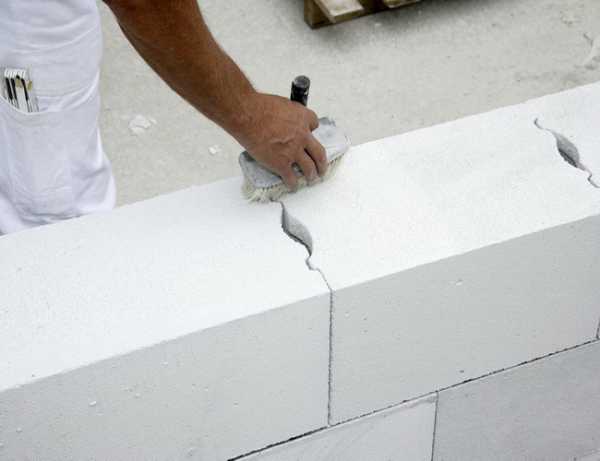
Плюсы газобетонных блоков и их минусы
Основные свойства описываемого материала настолько хороши, что являются важными его плюсами:
- Прочностью и долговечность. Чтобы эти характеристики проявились в полной мере, важно использовать материал правильно: для возведений зданий без каркаса и высотой не более четырнадцати метров. Также его можно смело применять для устройства внутренних стен и перегородок. По сроку службы блоки этого вида можно приравнивать к сроку службы кирпичей. Производитель дает гарантию в 80 лет.
- За счет общей легкости блоков нагрузка на фундамент сводиться к минимуму. Один блок заменяет при кладке двадцать кирпичей, это значит, что общее время работ и расход материала сокращается в несколько раз.
- Экологичность. Материалы основные только натуральные и чистые, сам по себе блок также показывает высокие экологические свойства. Вредных веществ он не выделяет. По способности пропускать воздух газобетон сравнивается с деревом. Стены из описываемого материала на ощупь всегда теплые за счет низкой теплопроводности.
- Устойчивость к огню. Проведенные исследования показали, что материал горение не поддерживается, так же, как и сам не горит. На газобетонную стену прямой огонь может воздействовать 3-7 часов и она устоит. Часто блоки этой категории используют, чтобы защищать от огня металлические конструкции.
- Морозостойкость, то есть, способность выдерживать полное замораживание и оттаивания. Мелкие поры материала вытесняют лед и воду. Поэтому около ста циклов сохранность газобетонного блока обеспечена. Если сравнить с кирпичом, он выдерживает только 25 циклов, а пенобетон – всего 35 циклов).
- Удобство обработки. Блоки из описываемого материала можно смело сверлить, колоть и резать. Причем, разрезаются блоки с помощью обычной ручной пилы.
Но любой строительный материал наравне с преимуществами имеет и свои недостатки. Его говорить про газобетон, то тут есть такие свои нюансы. Во-первых, не рекомендуется стоить здание выше трех этажей, потому что материал имеет ограниченную способность к сжатию. Во-вторых, требуется дополнительная внешняя облицовка стен, потому что материал активно впитывает влагу. К третьему минусу относится высокий коэффициент усадки (особенно, у неавтоклавного варианта).
Практически все характеристики описываемого материала являются отличными для строительства. Особенно надо обращать внимание на прочность, из-за которой газобетонные блоки лучше всего использовать для возведения построение не более четырех этаже в высоту.
Как выбрать качественные газобетонные блоки
При подборе стройматериалов важно знать и учитывать такие параметры как теплопроводность, плотность, прочность, звукоизоляция, огнестойкость.
При покупке важно сравнивать эти характеристики, потому что у разных производителей они могут отличаться:
- Коэффициент теплопроводности должен начинаться от 0,075 Вт/(м•К) для блоков плотностью D350 и от 0,25 Вт/(м•К) для блоков марки D700. В доме будет теплее, когда у используемого материала показатель этого коэффициента будет низким.
- Плотность в отношении массы к объему определяется марками от D300-350 до D1200 кг/м?. Чем выше показатель, тем более прочной будет конструкция, более хорошей будет звукоизоляция.
- Любые блоки этой категории должны обладают огнестойкостью, потому что они относятся к материалам негорючим. Перегородка из ячеистого бетона, уже отштукатуренная, в течение нескольких часов может выдерживать огонь не изменяя свой изначальный вид, не утрачивая характеристики.
- Газобетон должен быстро выветривать влагу и выводить водяной пар из помещения, которое отапливается.Чем выше индекс воздушного шума (определяется в дБ), тем лучшими звукоизоляционными свойствами обладает материал.
С появлением на рынке стройматериалов ячеистых бетонов расширились возможности застройщиков. Те уникальные свойства, которые присущи газобетону, грех не использовать при строительстве жилых и специальных объектов.
Есть ли вред для здоровья
Газобетонные блоки – это совершенно безвредный для здоровья человека материал. Несмотря на то, что материал этот искусственный, он производится из природных компонентов, которые являются совершенно безопасными. Экологичность придают те природные компоненты, из которых блоки состоят.
Этот материал активно используется в современном строительстве, он имеет несущественные минусы. Его можно смело использовать для зданий до четырех этажей высотой. Высота здания не имеет значения, если делать перегородки и несущие стены внутри помещения.
Возведение построек из газобетона сопряжено с некоторыми особенностями. Перед началом работ следует внимательно изучить не только свойства газобетона, но и технологию его укладки. Газоблоки укладываются намного проще, чем кирпичи или шлакоблок.
Из чего делают газоблоки?
Газоблоки – это современный строительный материал, отличающийся высоким качеством и надежностью. Но при этом такие изделия отличаются рядом отличительных особенностей.
Особенности газоблоков
Такой строительный материал отличается:
- отличной теплоизоляцией – он не пропускает холод в помещение и не выпускает тепло;
- пожаробезопасностью – такие изделия выдерживают воздействия высоких температур без повреждений;
- долговечностью – они не разрушаются с течением времени.
При всех своих преимуществах он еще и достаточно дешев в производстве, что делает его приоритетным выбором в большинстве случаев.
Как и из чего производятся газоблоки?
Технология создания газоблоков достаточно проста и включает в себя:
- воду;
- цемент;
- мелкий наполнитель;
- порообразователь.
Вода может использоваться самая обычная водопроводная или питьевая, но при этом в некоторых случаях предпочитают техническую воду. При этом она должна забираться из поверхностных источников, быть несоленой и иметь жесткость не выше средней, не содержать в своем составе различных примесей, в частности нефти, масел, жиров. Жидкость нагревается до 40-60 градусов, и эта температура поддерживается во время производства.
Также используется портландцемент марок М500Д0 и М400Д20. При этом нежелательно использовать продукцию, в которой содержатся минеральные добавки и вкрапления, отличающиеся гидрофобными характеристиками.
В смесь также добавляется песок, в качестве основного заполнителя. В роли наполнителей могут выступать различные минеральные добавки, в частности известняковая или доломитовая мука, получаемая с тепловых станций зола-унос, доменные шлаки или золошлаковые смеси.
Затем добавляется алюминиевый порошок, обеспечивающий образование пор. Дополнительно добавляется специальный порошок, который помогает частицам пудры распределиться по смеси.
В зависимости от требуемых характеристик могут быть дополнительные химические добавки. Они определяют скорость набора прочности, процесс газообразования или иначе изменяют готовое изделие.
Готовый и застывший массив газобетона отличается первое время достаточно пластичностью, чтоб провести его нарезку и придать необходимую форму. После этого в течение восьми часов он набирает прочность под специальным колпаком. Затем его можно использовать в строительстве, так как он отличается всеми необходимыми характеристиками.
www.hugebuilding.ru
Что такое газобетон?
Газобетон – энергосберегающий, современный материал, используемый для частного строительства, он отлично хранит тепло, обладает малой плотностью и массой, и как следствие легко обрабатывается и переносится. Что не мало важно – работать с газобетоном вполне может всего один человек, при этом за 1 день можно уложить около трех кубических метров и это без чьей-либо помощи, в одиночку!
Содержание статьи:
Что такое газобетон?
Что же такое газобетон? Так как больший объем материала отнимают газовые пузырьки ( они составляет около 85%, от общего объема материала) - то с «технической» точки зрения газобетон можно отнести к классу ячеистых бетонов.
Итак, мы отправляемся на один из самых больших заводов в России по объемам изготовления газобетона, в город Волжск на завод по изготовлению газобетонных блоков «Биктон» (BIKTON), который ведет свою историю с 2008 года. Что бы более детально ознакомиться с процессом изготовления этого строительного материала мы расскажем вам о нем в мельчайших подробностях.
Состав газобетона
Газобетон изготавливают из безопасного сырья:
- Около 60% - кварцевый песок;
- Приблизительно 20% - цемент;
- Еще 20% - это известь;
- И 1% - алюминиевая пудра;
Перечисленные ингредиенты перемешиваются с водой в заданной пропорции. Состав и качество исходных компонентов значительно влияют на прочность и другие характеристики конечного продукта.
Процесс производства
Подготовка основной смеси
Основой ячеистого бетона является песок, заранее обработанный в шаровых мельницах. Это выглядит приблизительно так: песок загружается в барабан мельницы, в котором располагаются чугунные шары. Во время вращения барабана они крошат песок, до тех пор пока он не превратится в «пыль».
Потом, это измельченное сырье отправляется на хранение в сберегательные бункера. В процессе изготовления, все ингредиенты будущих блоков: песок, цемент и известь тщательно перемешиваются.
Перед самой формовкой к полученной смеси добавляется алюминиевая пудра и вода. Полученная смесь наливается в прямоугольную форму – в которой будет формироваться пенобетон.
Реакция извести с алюминиевой пудры
Все самое интересное начинаться на данном этапе. Известь при смешивании с алюминиевой пудрой производит реакцию, при которой выделяется газ, он то и образует большое количество пузырьков. Диаметр полученных пустот от 0,5 мм. до 2 мм., а поскольку смесь тщательно перемешана, они равномерно распределяются по исходной массе.
Затем смесь выдерживается около трех часов, чтобы все компоненты смеси прореагировали между собой, после чего транспортер перевозит полученный блок на следующий этап.
Резка на блоки
Затвердевшую форму разделяют на равные блоки, разрезая форму поперек, а потом и по вдоль. На нашем заводе единовременно изготавливают блоки лишь одного размера. Чтобы получить блоки других размеров, производится перенастройка оборудования, заменяются ножи.
Всегда полный ассортимент готового продукта обеспечивает большой склад.
После того, как блоки были нарезаны в нужный размер транспортер отправляет сложенные блоки на дальнейший этап.
Интересный факт – завод «Биктон» работает круглосуточно, производство автоматизировано, и почти не нуждается в человеческом вмешательстве. Люди присутствуют лишь на этапе упаковки, на складе и в лаборатории проверки качества.
Выдержка в автоклаве
Далее блоки помещаются в автоклав, это важный этап, так как именно во время него все свойства блоков из газобетона улучшаются: повышается прочность, уменьшаются последующая усадка.
- Автоклавы достаточно вместительные: их длина около 30 метров;
- Блоки находятся в автоклаве около 12 часов при повышенном давлении около 12кг.\кв. см;
- В процессе они проходят обработку паром максимальная температура которого составляет 190 градусов Цельсия;
- После выхода из автоклава блоки еще влажные на 30%, через год хранения влажность составит 5-10%;
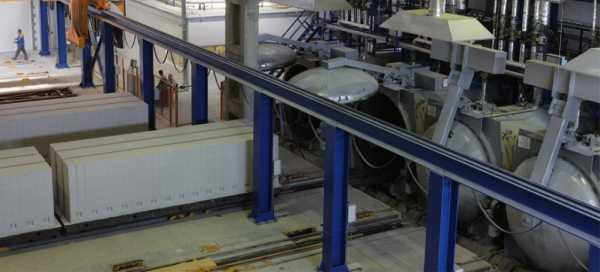
После этого каждая партия уходит в исследовательскую лабораторию для подтверждения соответствию заданным характеристикам. Испытания проводят на нарезанных кубиках – образцах по специально разработанной методике.
Блоки, прошедшие тест, укладываются на поддоны и оборачивается термоусадочной пленкой. Это предотвращает всякого рода порчу готового продукта, защищает их от влаги и механических повреждений.
Надежно упакованные блоки можно хранить прямо под открытым небом, это позволяет хранить большие объемы – что немаловажно для крупных корпоративных клиентов.
Чем отличается газобетон от пенобетона?
Теперь поясним чем же все-таки, отличаются блоки из газобетона от блоков из пенобетона.
Первое и самое очевидное, следует из названия:
- Пенобетон – изготавливается из пены, которая имеет в своем составе вредные химические вещества такие как: клей, канифоль, едкий натр и так далее.
- Газобетон – производиться с участием газа(водорода) образованного от химической реакции алюминиевой пасты и извести. Поэтому газобетон более экологически чистый, нежели пенобетон.
Второе, это то, что пенобетон не выдерживается в автоклаве и в следствии этого обладает низкими прочностными характеристиками. Если газобетон можно смело использовать для несущих стен, он морозостойкий, и теплый, то из пенобетона не рекомендуется строить ответственные несущие стены: он более холодный и будет промерзать.
И третье, это геометрия самого блока. При изготовлении пенобетона блоки не нарезают, а заливают сразу же в конечные формы, что во первых дает большую усадку материала: до 3-5мм.\м. после постройки, а во вторых блоки изначально имеют немного не ровные края.
Приобрести качественный газобетон на условиях самовывоза вы можете непосредственно на нашем заводе в городе Волжске. При необходимости вы можете заказать доставку в нашем отделе продаж.
10.02.2017
bikton.ru
плюсы и минусы достоинства недостатки
Функциональные, прочные и легкие в обработке материалы наиболее предпочтительны в строительной сфере. К сожалению, добиться такого сочетания эксплуатационных свойств непросто. Ячеистый бетон и в частности газобетонные блоки можно рассматривать как наиболее приближенный к таким требованиям стройматериал.
Его уникальная пористая структура позволяет сооружать теплые дома, которые при этом обладают высоким запасом прочности. Есть у ячеистых бетонов и минусы, поэтому в выборе такого средства строительства необходимо ознакомиться со всеми нюансами эксплуатации.
На современном рынке немало предложений по газобетону разных марок, что позволяет принять оптимальное решение при покупке.
Общие сведения о газобетоне
Как уже отмечалось, блоки из газобетона входят в группу ячеистых бетонов. Материал представляет собой готовые элементы для кладки стен и других конструкций.
Особенностью блоков является наличие в структуре пор, диаметр которых достигает 3 мм. Именно ячеистая структура определила одно из главных положительных качеств газобетона – эффективную теплоизоляционную функцию.
В основе блоков присутствуют такие компоненты как цемент, известь, гипс и кварцевый песок. Отдельно добавляются газообразователи, от которых во многом зависит качество газобетонных блоков, так как в процессе их действия и происходит формирование ячеистой структуры. Некоторые изготовители также вносят промышленные отходы, среди которых шлаки и зола.
Вернуться к содержанию
Технология изготовления
На первом этапе производится смешивание компонентов базового состава с водой. Таким образом готовится первичный раствор, который в дальнейшем заливается в специальные формы.
Далее следуют реакции с выделением водорода. Ее провоцирует внесенный газообразователь и гидроксид кальция. Так происходит вспучивание массы, в результате чего увеличивается ее объем. Когда смесь достаточно затвердеет, ее вынимают из формы и обрабатывают механическим способом.
На этой стадии из монолитной основы получают те самые газобетонные блоки или панели. В дальнейшем технологии изготовления предполагают разные операции – например, блоки могут обрабатываться водяными парами или проходить сушку в специальных камерах.
Завершающая обработка может производиться по автоклавной или неавтоклавной методике. В сущности это разновидности способов отвердевания.
Российские компании выпускают автоклавные газобетонные блоки на основе извести, а неавтоклавные – из цемента. Отличия между технологиями обеспечения твердения заключаются в том, что автоклавные материалы проходят этот процесс в камерах-автоклавах при повышенном давлении и температуре. Неавтоклавные блоки не подвергаются обработке от специальных сред и затвердевают в естественных условиях, но при тепловлажностном воздействии.
Вернуться к содержанию
Где применяется?
Блоки из газобетона используются практически во всех сферах строительства. Другое дело, что его физико-технические качества накладывают определенные ограничения в процессе монтажа. Так или иначе, материал используют в строительстве жилых домов, зданий коммерческого назначения, промышленных и производственных объектов.
В строительстве многоэтажных жилых домов из газобетона сооружают несущие комбинированные стены и внутренние перегородки. К слову, податливость в обработке позволяет разнообразить архитектурные идеи при строительстве стен.
В малоэтажном строительстве газобетонные блоки плюсы и минусы которых были правильно рассчитаны, могут использоваться и как материал для наружных стен. Как правило, это одно- и двухэтажные постройки, но если речь идет о каркасно-монолитных проектах, то этажность неограничена – в таких случаях из газобетона формируются перегородки и фасады.
Исходя из вышесказанного, можно резюмировать, что блоки из газобетона в основном применяются как основа для стен. Однако в зависимости от конструкционного исполнения и типоразмера этот материал может выступать как теплоизоляционный барьер в отделке тех же стен и перегородок.
Вернуться к содержанию
Разновидности газобетона
Одно из ключевых разделений по видам газобетона обусловлено технологией производства. Это уже отмеченные автоклавные и неактоклавные блоки. Отличаются данные стройматериалы двумя качествами: теплопроводность и прочность на сжатие. Метод автоклавной постобработки является усовершенствованным и позволяет получить материал с повышенной теплоизоляцией и долговечностью.
Не менее значима и классификация по назначению, от которой следует отталкиваться в первую очередь при выборе материала для определенных целей.
Блоки из газобетона бывают конструкционными, теплоизоляционными и комбинированными, в которых совмещены первые две функции. Соответственно, конструкционные используются для кладки стен, комбинированные – для формирования стен и перегородок с утеплением, а теплоизоляционные рассчитаны сугубо на решение задач утепления строительных конструкций.
Следующая классификация предполагает более углубленный анализ характеристик газобетона. В данном случае рассматриваются свойства вяжущего компонента, который используется в процессе создания блоков. В качестве этой добавки может применяться известь-кипелка, гипс, шлаки, цемент с определенной долей портландцемента, зольные и кремнеземистые элементы.
Вернуться к содержанию
Марки блоков из газобетона
Среди наиболее популярных марок стоит выделить D350, D400, D500 и D600. Материал под маркой D350 является довольно редким, так как его эксплуатационные характеристики могут обеспечить и многие другие стройматериалы. Тем не менее, его легкость, низкая теплопроводность и доступность в обработке позволяют использовать блоки в качестве неплохого теплоизолятора.
Марка D400 располагает более высокими показателями прочности (до 1,5 МПа), что позволяет использовать такой материал при кладке стен с небольшими нагрузками. Функция теплоизолятора в таких блоках также сохранена, поэтому с их помощью можно создать прочную защиту от теплопотерь.
Наибольшей популярностью в строительстве пользуются марки газобетонных блоков с обозначением D500. Такие блоки обладают оптимальными для своего класса характеристиками прочности, огнеупорности и морозостойкости. В частности, прочность на сжатие до 3 МПа позволяет возводить перекрытия в монолитных домах и внешние стены в малоэтажных постройках. По сравнению с маркой 350, такой газобетон также отличается повышенной шумоизоляцией, хотя в плане теплопроводности незначительно уступает более легкому аналогу.
Газобетонные блоки с маркировкой D600 демонстрируют прочность до 4,5 МПа. Этот показатель позволяет непросто использовать блоки в сооружении стен и перегородок жилых домов разной высотности, но и предусматривать более высокие нагрузки. В частности, к стенам из материала этой марки можно крепить вентилируемый фасад.
Вернуться к содержанию
Преимущества газобетонных блоков
Газобетонный материал является весьма привлекательным и в плане удобства монтажа, и в отношении эксплуатационных качеств. Этому способствуют следующие качества:
- Теплоемкость. Газобетон хорош не только при эксплуатации в качестве теплоизолятора, но и в целом как энергосберегающий материал. Именно пористая структура позволяет обеспечивать теплосбережение, которое в несколько раз превышает аналогичные качества традиционного бетона и кирпича;
- Небольшая масса при высокой прочности. Конечно, по сравнению с камнем и кирпичом газобетонный блок не так прочен, однако, в своей области применения этих показателей достаточно. Средняя плотность, которая обусловлена пористой структурой, наделяет материал скромной массой. В итоге облегчается транспортировка и работа строителей;
- Паропроницаемость. Материал регулирует влажностный режим в помещениях, рационально впитывая и отдавая влагу;
- Огнестойкость. Неорганическое происхождение газобетона делает его негорючим стройматериалом. Как и металлические конструкции, он может применяться в строительстве жилых домов и промышленных объектов с повышенными требованиями к пожаробезопасности;
- Звукоизоляционные качества. Опять же, пористая структура формирует эффективный барьер, оказывающий сопротивляемость шуму и звукам;
- Легкость кладки. Процесс монтажа облегчается благодаря нескольким факторам. Во-первых, блоки имеют точную форму и геометрию, не требуя особых манипуляций с выравниванием кладки. Во-вторых, работы упрощаются и благодаря небольшому весу газобетона как такового. И в-третьих, материал укладывается не на бетонный раствор, а на специальный клей;
- Легкость в обработке. В этой характеристике строители иногда сравнивают газобетон с древесиной. Блоки и плиты без труда поддаются резке обычным слесарным инструментом, при этом операции выполняются практически без отходов;
- Сейсмостойкость. Небольшая масса газобетонных блоков в комбинации с оптимальными показателями прочности в целом нивелируют действия оказываемых нагрузок. Маленький вес и надежность таких стен делают дома из газобетона стойкими не только перед землетрясениями, но и перед другими катастрофическими природными явлениями. Кстати, если регион изначально предрасположен к сейсмическим угрозам, то следует при строительстве дома из таких блоков предусмотреть и включение армирующих элементов;
- Морозоустойчивость. В этом случае многое зависит от технологии производства. Например, газобетонные блоки изготовление которых осуществлялось с применением автоклавного оборудования, в меньшей степени подвержены заполнению водой своей полости. Сама структура пор не позволяет им наполняться жидкостью. Следовательно, и циклы замораживания не оказывают серьезных нагрузок на материал;
- Экологичность. В рецептуре для производства газобетонных блоков присутствуют в основном минеральные экологически чистые компоненты. В их числе песок, вода, известь, цемент, различные шлаки и т.д. Среди искусственных элементов можно отметить только связующие компоненты, но их процент незначителен с точки зрения нанесения вреда человеку. Особенно в этом плане безопасны автоклавные блоки, так как процедура принудительного твердения позволяет избавить материал от вредных примесей.
Вернуться к содержанию
Недостатки газобетонных блоков
Учитывая все вышеописанные достоинства можно сделать вывод, что ячеистый бетон и вовсе не имеет аналогов на современном рынке стройматериалов. Однако, газобетонные блоки плюсы и минусы которых делают их довольно специфическим материалом, имеют и серьезные ограничения в применении. Это обусловлено, пусть немногочисленными, но серьезными недостатками, в числе которых следующие:
- Низкая влагостойкость. Несмотря на то, что поры автоклавных блоков не заполняются водой, это не исключает вредного воздействия последней на структуру материала. В результате дома, стены и перегородки из газоблоков нуждаются в качественной самостоятельной гидроизоляции;
- Подверженность усадке. Процессы усадки свойственны практически всем материалам, которые закладываются в основу зданий любого типа. Но в случае с газобетонными блоками важно учитывать последствия усадки в виде образования трещин. Производители стремятся минимизировать их, но небольшие смещения до 3 мм все же имеют место. Избавиться от усадки можно только с помощью грамотной сушки блоков перед их использованием.
Вернуться к содержанию
Вывод
Газобетонные блоки можно отнести к неоднозначным стройматериалам. Это значит, что такие блоки имеют довольно весомые преимущества, но при неправильном использовании могут свести на нет все усилия строителей.
С другой стороны, это легкий и экономичный материал. Например, отделка газобетонных блоков необязательна, что снижает расходы, как и в случае с транспортировкой материала.
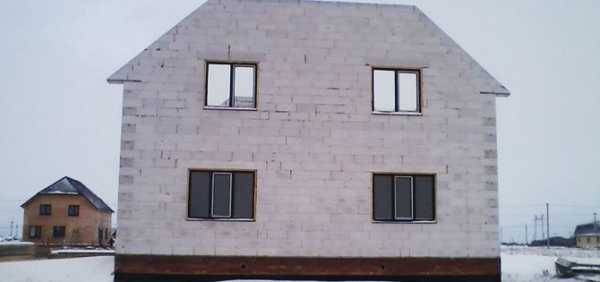
Из-за недостаточной прочности даже незначительная усадка может спровоцировать образование трещин в блоках. Поэтому обязательным мероприятием в ходе проектирования должен стать скрупулезный расчет характеристик ячеистых блоков и, что особенно важно, оценка их прочностных показателей.
Не нашли ответов в статье? Больше информации по теме:
dachaorg.ru
Как сделать газобетон своими руками. Делаем сами. mstyle-fur.ru
Из чего состоит газобетон
Газобетон – это искусственный камень, который используют для возведения стен в индивидуальном строительстве. Он подходит для сооружения несущих конструкций, внутренних перегородок и заполнения межкаркасных пространств. Газоблоки не дают большой нагрузки на фундамент, поскольку имеют ячеистую структуру и малый вес. Это экономичный стройматериал, обладающий высокими теплоизоляционными свойствами.
Состав и способ получения газобетона
Существует несколько типов классификации ячеистого бетона: в зависимости от назначения, формы, технологии производства и состава.
1. По способу обработки различают автоклавный и неавтоклавный газобетон.
2. По назначению газоблоки могут быть теплоизоляционным, конструкционным или конструкционно-теплоизоляционным. Они имеют определенную маркировку, например, газобетон d500 относится к классу конструкционно-теплоизоляционных блоков.
3. По форм-фактору делятся на U-образные, прямые и паз-гребневые.
Газоблоки изготавливают из песка, цемента, извести, воды, гипса и алюминиевой пудры. Также в производстве могут использоваться вторичные и побочные промышленные материалы, такие как шлак и зола. В зависимости от состава газобетона, его классифицируют на:
В искусственно синтезированный камень строительная смесь преобразуется лишь при определенных условиях. Для его получения используют технологию автоклавного затвердения. В этом случае состав застывает под влиянием насыщенного пара и высокого давления, меняя свою структуру. В смеси образуется минерал тоберморит, который придает материалу прочность. Таким образом получают автоклавный газобетон.
Бетон, затвердевающий в естественных условиях, называют неавтоклавным. Он имеет ячеистую структуру, но отличается по своим свойствам от газоблоков, изготовленных по специальной технологии. Этот стройматериал больше подвержен усадке при эксплуатации, поэтому его целесообразно применять в случае небольших нагрузок. Чтобы увеличить прочностные характеристики неавтоклавных блоков, в исходный состав добавляют различные армирующие вещества и наполнители. Снизить усадочную деформацию позволяет применение полиамидных пластмасс при армировании.
Производство неавтоклавных блоков не требует дорогостоящего оборудования, поэтому их можно сделать самому.
Газобетон своими руками
Процесс производства состоит из нескольких этапов:
- подбор и смешивание компонентов;
- заполнение форм раствором;
- выдержка состава для набора прочности;
- извлечение из форм.
В универсальном составе для получения газобетона содержится цемент, песок, известь, алюминиевая пудра. Исходные добавки и их пропорции могут меняться, в зависимости от наличия сырья и требований к готовому стройматериалу. Например, в автоклавном производстве песок иногда заменяют золой или шлаком. А для получения стройматериала с меньшей плотностью можно делать газобетоны на основе смол ТЭС.
При изготовлении газобетона в домашних условиях необходимо правильно рассчитать соотношение расходных материалов и учесть особенности укладки и погрешности замеров. Но существуют и стандартные рецепты смеси для газоблоков, в которых указаны следующие пропорции:
Данные вещества используются и при автоклавном производстве. Ориентируясь на приведенное в рецептуре соотношение, можно рассчитать приблизительное количество компонентов, которые войдут в состав на 1 м3 газобетона:
- Портландцемент – 90 кг;
- Вода – 300 л;
- Газообразователь – 0,5 кг;
- Известь – 35 кг;
- Песок – 375 кг.
Однако идеального состава в домашних условиях можно добиться лишь опытным путем, поскольку многое зависит от качества исходных компонентов. Повлиять на течение химической реакции может как температура воды, так и марка цемента.
Инструкция по самостоятельному изготовлению неавтоклавного газобетона
Для получения газоблока дома не потребуются сложная аппаратура и инструменты. Главное – четко следовать пунктам приведенного ниже пошагового руководства и использовать компоненты в определенном соотношении, а не на глаз.
1. Исходя из указанных пропорций вычислить необходимое количество ингредиентов.
2. В первую очередь, необходимо смешать портландцемент с предварительно просеянным песком.
3. В полученную смесь влить воду и все тщательно перемешать.
4. Добавить в раствор другие компоненты. Алюминиевая пудра всыпается в последнюю очередь. В приготовлении как неавтоклавного, так и автоклавного газобетона одинаково важен процесс смешивания ингредиентов. Для равномерного распределения воздушных пузырьков лучше использовать бетономешалку.
Действительно рабочий законный способ экономии.Это нужно знать каждому!
5. Полученный раствор разливается в специальные формы, которые изготавливаются из металлических листов или деревянных досок. Чтобы застывший газобетон было легче достать, лучше использовать разборные конструкции. Кроме того, форму рекомендуют смазывать машинным маслом, разведенным с водой.
6. Заливать смесь нужно наполовину, поскольку она в процессе химической реакции расширяется практически вдвое. Этот процесс занимает около шести часов, после чего можно выравнивать блоки, срезая выступившую массу.
Формирование в этом случае длится дольше, чем для автоклавного газобетона – требуется не менее 12 часов, чтобы смесь затвердела. Для ускорения процесса застывания состава рекомендуют добавить растворимые соединения натрия (соду) на этапе приготовления раствора. Марочную прочность материал набирает после 28 дней выдержки. Готовый неавтоклавный газоблок, приготовленный своими руками, подходит для малоэтажного строительства, например, для возведения одноэтажного дома или гаража.
Как сделать газобетон своими руками?
В начале строительных работ возникает вопрос: какой материал наиболее долговечный, надежный и выгодный в плане финансов? Предлагаем альтернативное решение – наладить производство газобетона своими руками. В самом начале важно понять, что такое газобетон, какими свойствами обладают такие блоки, а также область применения. Итак, будем изучать вопросы по порядку перед тем, как сделать выбор.
Описание, виды и характеристики
Газобетонный блок – это искусственный строительный материал, полученный путем смешивания различных природных компонентов. Высокая прочность и пористая структура с отличными теплоизоляционными свойствами позволяют использовать материал для строительства жилых помещений.
Организация производства газобетона в домашних условиях позволяет изготавливать искусственный камень с любой необходимой геометрией
В сравнении с другими стройматериалами для возведения стен он имеет небольшой вес, используется для кладки внешних, несущих стен здания, а также межкомнатных перегородок. Применяется в монолитном строительстве для заполнения проемов.
Газобетонные блоки делят на три вида:
- конструкционные;
- теплоизоляционные, применяют для внутренних перегородок;
- конструкционно-теплоизоляционные.
По форме изделия выделяют:
- прямоугольные блоки – для несущих и внешних стен;
- блоки перекрытий, или армированная газобетонная балка – для потолков;
- для монтажа оконных и дверных проемов Т-образная или U-образная форма изделия.
Основные составляющие
Рассмотрим состав, а также оборудование для проведения работ по изготовлению газобетона.
Покупка готовых блоков, с учетом доставки их на место, обойдется значительно дороже
Материал или ингредиенты для газобетона:
Все материалы, которые используются в изготовлении газобетона, не выделяют токсических веществ. Благодаря этому стройматериал безопасен для здоровья людей и может быть использован для постройки жилых помещений. Качественное оборудование и доступные компоненты делают процесс производства газобетона быстрым и удобным.
В последние годы такая продукция имеет повышенный спрос с возрастающими процентами продаж. Часто оборудование для изготовления газобетона становится стартом – началом собственного бизнеса со стабильным доходом.
Производство газобетона своими руками – альтернативное решение для тех, кто имеет много свободного времени и стремится сэкономить на материале для постройки дома.
Изучаем технологию
Производство начинается с подготовительных этапов:
- собираем и устанавливаем форму, внутренние стенки которой нужно обязательно обработать смазочным материалом, чтобы избежать прилипания массы к форме. Материалом, из которого изготавливают формы, служит дерево, или металл;
Плюс – отвердевание происходит естественным путем
- подготавливаем основные составляющие для газобетона. Соответственно пропорции готовим массу, производим заливку в форму, и отправляем в так называемую зону созревания. Сначала масса увеличивается в объёмах. На этом этапе газобетон приобретает пористость. Происходит химическая реакция алюминиевой пудры и извести. Заливочная масса равномерно насыщается пузырьками водорода, размером до 2мм;
- этап резки, заключается в распилке большого за размером массива (6160 мм x 1580 мм x 690 мм) на меньшие части. Происходит снятие горбушки и выравнивание поверхности проволочными струнами;
- отправляем сформированные блоки для дальнейшей просушки и затвердевания естественным способом.
На что обратить внимание?
Критерии, которые служат ориентиром при выборе газобетонных блоков в строительстве:
- невысокая стоимость готового изделия. Возможность сделать газобетонные блоки своими руками, купить оборудование для обычного потребителя не составит проблем;
- высокая прочность при небольшом весе. Размер стройматериала позволяет делать качественную кладку в короткие сроки. Кирпичи количеством 20 штук = 1 газобетонному блоку;
- не подвергаются процессам старения и гниения. Состоят из природных материалов, обладают способностью пропускать воздух;
- высокий коэффициент теплоотдачи способствует продуктивному сбережению тепла в период отопления. Уменьшает уровень теплоизоляционных работ готового строения;
- невысокая нагрузка на фундамент, не дают усадку;
Этот этап всегда является самым сложным. И дело не в качестве перемешивания, а в долевом соотношении ингредиентов
- легко поддаются обработке. Необходимость подрезать, утончить и просверлить не составит проблемы. Ручная пила станет инструментом, который легко справится с такой задачей;
- обладают высокой устойчивостью к воздействию прямого огня;
- газобетон способен выдерживать мороз и оттаивание до 100 циклов – в два раза больше, чем кирпич.
- высокий уровень звукоизоляции при использовании межкомнатных перегородок и несущих стен;
- уровень поглощения воды в сравнении с кирпичом 1:1.
Как применить на практике?
Построить дом или здание в короткий промежуток времени с применением современных материалов – реально. Специалисты в категории строительных работ отмечают, что газобетон – доступный по цене и качественный по всем стандартам материал, который используется для:
- жилых домов;
- подсобных хозяйских помещений;
- гаражей;
- складских помещений;
- магазинов;
- зданий для частного бизнеса.
Как сделать правильный выбор?
Итак, решение принято – стены запланированного сооружения будут из газобетона, определяем что выгоднее:
- Подсчитываем общую стоимость материала и делаем закупку.
- Принимаем взвешенное решение, чтобы приобрести все необходимое и наладить производство газобетона своими руками.
Найти надежного партнера, который предложит качественный товар, можно, воспользовавшись услугами нашего сайта. Осуществить закупку соответствующих материалов и оборудование для начала работы можно на протяжении одного дня, без лишней суетливой беготни по магазинам. Правильный состав и выдержка технологического процесса, принесут долгожданные плоды. Наладить мини-бизнес по производству газобетона или собственных надобностей – приятная работа с очевидным результатом.
Газобетонные блоки своими руками
«Как сделать газобетон своими руками и возможно ли это вообще?», — таким вопросом задаются многие дачники. Технология изготовления неавтоклавного пористого (его ещё называют ячеистым) бетона в домашних условиях не представляет собой сложного процесса. Смесь состоит из материалов, которые широко представлены в продаже, а условия созревания смеси нормальные и не требуют специального оборудования. Использование в строительстве самодельных изделий из ячеистого бетона позволяет ощутимо сэкономить на стройматериалах, они обходятся примерно на 30% дешевле заводских, но требуют дополнительных затрат времени на их изготовление. Газобетон имеет свои плюсы и минусы, к плюсам относятся низкая теплопроводность, малая плотность, высокая огнестойкость и хорошая звукоизоляция. К недостаткам можно отнести высокую гигроскопичность (способность к поглощению влаги), хрупкость и недекоративный внешний вид, что требует дополнительной отделки стен.
Материалы, необходимые для изготовления в домашних условия газобетонных блоков:
- Портландцемент марки М400 – М500.
- Негашёная известь.
- Алюминиевая пудра.
- Мелкий, мытый и тщательно просеянный речной песок.
- Эмульсия для смазки форм или отработанное машинное масло, разведённое водой в пропорции 1:3, эмульсию следует приготавливать каждый раз непосредственно перед каждой заливкой блоков.
Также потребуется следующий инструмент и оборудование для производства газобетона:
- Бетономешалка или миксер с электродрелью, так как вручную невозможно добиться однородности смеси.
- Стальная струна или проволока для срезания излишков смеси.
- Мастерок.
- Молоток.
- Металлические инвентарные (они имеются в продаже) или сделанные самостоятельно формы для заливки блоков.
- Мерное ведро.
- Гладилка.
- Кисть для нанесения эмульсии.
Самостоятельно изготовленные формы для заливки представляют собой сделанный из металлического листа или досок короб, разбитый перегородками на ячейки в размер будущих газобетонных блоков. Сверху необходимо предусмотреть крепящуюся к стенкам короба на зажимах или болтах крышку. Обычный (заводской) размер изделий из газобетона: длина – 600 мм. высота – 250 мм. ширина – 200/250/300/350/400/500 мм. Толщина стенок короба, в случае изготовления его из досок, должна иметь толщину не менее 30–40 мм. так как в процессе схватывания смесь имеет свойство значительно увеличиваться в объёме. Внутренние перегородки возможно изготовить из фанеры (желательно влагостойкой) толщиной 12–16 мм. Лучше всего сделать короб разборным, на болтах, для удобства извлечения готовых изделий. Практика показывает, что оптимальный размер короба должен позволять заливку одновременно не более 6–9 блоков, иначе он получится слишком габаритными и тяжёлыми. Таких коробов следует изготовить несколько для непрерывности процесса заливки изделий. Технология производства газобетона по своей сути основана на реакции окисления алюминиевой пудры при контакте с водой в результате которой происходит бурное выделение углекислого газа. Если эта реакция проходит внутри закрытой формы в среде вязкой массы, то газ образует поры в смеси по всей её толще. После схватывания такой смеси в нормальных условиях получают бетон с закрытыми круглыми порами размером 1–3 мм.
Для начала в подготовленной ёмкости тщательно смешивают сухие компоненты, добиваясь того, чтобы пудра равномерно распределилась по всему объёму. Предварительно нужно немного поэкспериментировать с пропорциями компонентов смеси для получения наиболее качественных изделий.
Рекомендуемые объёмные пропорции смеси таковы:
- Цемент М400 (М500): 20%.
- Негашёная известь: 20%.
- Песок: 59%.
- Алюминиевая пудра: 1%.
Вода – в количестве, достаточном для получения раствора в консистенции негустой сметаны Воду, предварительно разогретую до температуры 40 градусов Цельсия, заливают во вращающуюся бетономешалку, следом высыпают приготовленную смесь. После тщательного перемешивания до получения однородной смеси, по консистенции похожей на негустую сметану, производят заливку горизонтально установленных форм до половины. Это обусловлено тем, что в процессе застывания, из-за протекающих химических реакций, смесь будет увеличиваться в объёме. Для облегчения извлечения готовых блоков, внутреннюю поверхность формы предварительно смазывают эмульсией, получаемой методом смешивания машинного масла с водой в пропорции 1:3. Процесс увеличения объёма протекает в течение 10–15 минут, через некоторое время смесь начнёт опускаться вниз. После прекращения «брожения», это занимает около 5–6 часов, выступающие излишки материала срезаются стальной струной, сверху формы накрываются крышкой и укрываются теплоизоляционным материалом. В таком состоянии раствор оставляют на сутки для полного затвердевания. По прошествии указанного времени газобетон извлекается из формы и укладывается на деревянные поддоны для полного затвердевания (набора марочной прочности), данный процесс занимает 28 суток. После этого блоки готовы к применению их в строительстве.
Дополнительно, для обеспечения качества изделий, нужно придерживаться следующих рекомендаций:
- Формы должны устанавливаться на твёрдую горизонтальную поверхность, для выдерживания геометрических размеров блоков.
- Помещение, где производятся работы по заливке, должно быть тёплым.
- Важно исключить любую возможность сквозняков.
Если в домашних условиях изготовить дополнительные вкладки, то можно отливать изделия разных размеров и конфигураций, необходимых для именно данного строения. Это позволит впоследствии уменьшить затраты времени на подгонку одинаковых газобетонных блоков по месту.
Источники: http://stroitel-list.ru/bloki-i-plity/gazobeton/iz-chego-sostoit-gazobeton.html, http://pobetony.ru/vidy-betona/proizvodstvo-gazobetona-svoimi-rukami/, http://kamedom.ru/gazobeton/gazobeton-svoimi-rukami.html
Комментариев пока нет!mstyle-fur.ru
Как делают газобетонные блоки
Газобетон самый популярный материал для возведения стен на рынке загородного домостроения. Сегодня как минимум три из пяти домов строятся именно из этого материала. О том, как делают этот недорогой, но теплый и прочный материал, пойдет речь в данной статье.
Газобетон — самый доступный материал для возведения стен. Кубометр газобетона почти в два раза дешевле кубометра профилированного бруса, притом что, как и дерево, он одновременно является и конструкционным, и теплоизолирующим материалом. С точки зрения теплосбережения, стена из газобетонных блоков будет почти в два раза теплее деревянной при той же толщине.
Высокая точность геометрии блоков, отклонения по которым составляет менее миллиметра, позволяет класть стену из газобетонных блоков на специальный клей, при использовании которого толщина швов составляет порядка 1–2 миллиметров. Это позволяет избавиться от мостиков холода, которые неизбежно возникали бы, если бы толщина швов составляла 1–2 сантиметра, как в случае с кирпичной кладкой.
Точная геометрия блоков, в сочетании с их относительно большими размерами и низким весом, существенно упрощает и ускоряет работу по возведению стен, благодаря чему с ней могут справиться каменщики даже не самой высокой квалификации. Так, одна бригада из трех человек вполне может возводить по 50 квадратных метров стены за смену. То есть, внешние стены одноэтажного дома с размерами 8×8 метров можно сложить всего за три дня.
Низкий вес газобетонных блоков, которые при плотности D400 в полтора раза легче дерева, обеспечивает снижение веса всего дома, что позволяет существенно экономить на фундаменте.
Однако, при всех своих достоинствах, газобетон не является абсолютно идеальным строительным материалом. Дому из газобетона нужен пусть и не с чрезмерной несущей способностью, но стабильный бетонный фундамент, части которого не будут иметь сезонных смещений относительно друг друга. Обратной стороной прочности газобетона, которая достаточна для строительства четырех- и даже пятиэтажного здания, является его хрупкость, так что блоки нельзя ронять и, учитывая качество наших дорог, транспортировать более чем на 300 километров. Но главная проблема состоит в низкой просвещенности и, как следствие, неправильном понимании свойств этого материала некоторыми строителями. Газобетон — это очень теплый стеновой материал, удовлетворяющий всем нормам по энергоэффективности и совершенно не нуждающийся в каком-либо дополнительном утеплении. Тем не менее, строители очень любят производить внешнее утепление домов из газобетона паронепроницаемыми утеплителями, такими, например, как пенополистирол. Дело в том, что газобетон, как и дерево, это паропроницаемый материал, то есть сквозь него осуществляется прохождение насыщенного водяными порами воздуха, стремящегося выйти из теплого помещения на холодную улицу. Если на пути паров встает паронепроницаемая преграда в виде пенополистирола, то в толще газобетона начинается процесс влагонакопления, который в свою очередь существенно повышает его теплопроводность и создает условия для возникновения плесени. Таким образом, после этого якобы утепления дом через какое-то время становится не теплее, а холоднее, чем был до этого. Значительно эффективнее было бы потратить дополнительные средства на утепление перекрытий, а также установку теплосберегающих окон и дверей.
Очевидно, что минусы, имеющиеся у газобетона, не могут затмить его достоинств, тем более что при грамотном ведении строительных работ их можно легко обойти.
Газобетонные блоки — это высокотехнологичный строительный материал, который с должными показателями по плотности, прочности и точности габаритных размеров можно изготовить только на современном заводе со сложным производственным циклом. Только выверенная дозировка составляющих, изменяющаяся в зависимости от свойств каждой партии сырья, в сочетании с точным соблюдением всех технологических циклов может обеспечить стабильное качество газобетона. Чтобы убедиться в объективности всех достоинств этого материала, давайте проследим цикл его изготовления от поставки сырья и до отгрузки готовых блоков покупателям.
1. Только с помощью аэрофотосъемки можно объективно оценить размеры завода по производству газобетона. | ||
2. Начинается всё с лаборатории, в которую попадают образцы из каждой поступающей партии сырья. | ||
3. В большом ангаре хранятся кварцевый песок и гипсовый камень. Погрузчик загружает их в специальную мельницу. | ||
4. Огромный вращающийся барабан мельницы заполнен металлическими шариками, с помощью которых осуществляется измельчение и перемешивание исходного сырья. | ||
5. Управляется мельница с компьютерного пульта, на экране которого благодаря датчикам мельницы можно отслеживать стадии помола. | ||
6. В высоких силосах хранятся цемент и негашеная известь — еще одни составляющие для производства газобетона. | ||
7. Все процессы на заводе роботизированы и управляются с компьютерного пульта, без непосредственного участия человека. | ||
8. Все составляющие смешиваются между собой, после чего в них добавляется вода и алюминиевая пудра, которая при реакции с негашеной известью выделяет водород. Он и формирует структуру газобетона. Полученная смесь помещается в специальную форму на железнодорожной тележке. | ||
9. Смесь в форме вспучивается при температуре 60 градусов и застывает, превращаясь в геометрически стабильную газобетонную массу, после чего поступает в цех на дальнейшую обработку. | ||
10. Газобетонная масса вынимается из формы и ставится вертикально, после чего контролер с помощью специальных приборов снимает ее параметры. | ||
11. Газобетонная масса ровно разрезается специальными струнами. | ||
12. Следующий станок делает вертикальный рез и с помощью фрезеровки формирует захваты для рук. | ||
13. Массив нарезанных блоков переворачивается обратно в горизонтальное положение. | ||
14. На специальной вагонетке блоки отправляются в автоклав. | ||
15. Под действием влажности и температуры в автоклаве блоки приобретают необходимую прочность и всем знакомый светло-серый цвет. | ||
16. Массив блоков после автоклава опять ставится вертикально и поступает на линию упаковки. | ||
17. Захват робота отделяет от массива соответствующее одной паллете количество блоков. | ||
18. Следующий робот надевает на газобетонные блоки термоусадочную пленку, которая предохранит их от атмосферных воздействий и обеспечит целостность паллеты во время транспортировки. | ||
19. Готовые паллеты с блоками поступают на склад, откуда отгружаются покупателям. | ||
zdspb.ru
Стены из газобетона своими руками | Своими руками
Реклама
Свойства газобетона
Сырьевыми компонентами для производства газобетона служат песок, известь, цемент, вода и алюминиевая паста. Отформованная масса пропаривается под давлением в автоклавных установках при температуре 180-200 °С, в результате чего твердеет. Материал изготавливают в виде блоков, в том числе крупноформатных и обладающих нестандартной формой.
На нашем рынке он представлен продукцией марок Ytong (Германия), AeroStone, Bonolit, EuroBlock, Poritep, «Грас» (все – Россия) и др. У газобетона целый ряд достоинств, среди которых – высокая прочность на сжатие, хорошая паропроницаемость, экологическая и пожарная безопасность, хорошее звукопоглощение, простота обработки (легко режется специальной ножовкой).
Но главный плюс газобетона – отличные теплозащитные свойства, что позволяет строить из него здания с однослойными наружными стенами малой толщины. То есть не требуется дополнительно утеплять ограждающие конструкции тем или иным теплоизоляционным материалом, срок службы которого будет, скорее всего, меньше срока службы самих конструкций.
При сооружении в средней полосе России коттеджа высотой до 4 этажей большинство производителей рекомендует для наружных стен применять блоки толщиной 375 мм и плотностью марки D500. Теплотехнические свойства ограждающих конструкций из таких блоков в сочетании со штукатурной отделкой почти соответствуют требованиям СНиП 23-02-2003 «Тепловая защита здания» по сопротивлению теплопередаче (R0) стены в этом регионе (не стоит забывать и о том, что те-плопотери через стены значительно меньше, чем через окна, двери, крышу, фундамент, подвал). Некоторые производители выпускают блоки плотностью D400, которые обладают необходимой несущей способностью, но при этом обеспечивают величину R0, превышающую требования СНиПов (чем меньше плотность блока, тем лучше его теплозащитные характеристики).
Читайте также: Строительство дома из керамоблоков
Фундамент для дома из газобетона
Вес здания из газобетона значительно меньше, чем из других каменных материалов (в частности, из крупноформатного кирпича), а потому и нагрузка на фундамент ниже. Понадобится менее массивный фундамент, а значит, расходы на его сооружение также будут меньше. Однако у газобетона сравнительно низкая прочность на изгиб, и, чтобы избежать появления трещин в стенах дома, необходимо создать надёжное основание под кладкой.
Опирание железобетонной плиты на стену из газобетонных блоков:1. Газобетонный блок2. Внутренняя отделка3. Выравнивающий слой из цементнопесчаного раствора4. Слой эффективной теплоизоляции5. Монолитная железобетонная плита6. Доборный газобетонный блок7. Наружная отделка
Тип и конструктив фундамента выбирают в соответствии с геологическими исследованиями грунта и расчётными нагрузками на основание. Возможно возведение фундаментов любых типов.
Отметим, что самым экономичным и быстро реализуемым решением можно считать сборное основание в виде ленты из блоков ФБС, заложенное на глубину промерзания грунта.
Готовые крупноформатные блоки устанавливают с помощью крана, и сразу после их укладки можно приступать к сооружению стен. Другой сравнительно недорогой и быстровозводимый вариант основания – буронабивные сваи с железобетонным ростверком.
Комментарий
«Среди ошибок, допускаемых при возведении стен из газобетона, – укладка блоков на обычный цементно-песчаный раствор вместо специального клеевого состава, рекомендованного производителем газобетона. Обычный раствор предполагает толстый шов (10-15 мм), что приводит к существенным теплопотерям через кладку (при отсутствии дополнительного утепления). Зачастую на вертикальную часть блока наносят слой клеевого состава меньшей толщины или не наносят его вообще, что ухудшает эксплуатационные свойства стены. Блоки необходимо укладывать с перевязкой размером не менее 110 мм для передачи нагрузки от блока к блоку Отсутствие такой перевязки чревато появлением трещин в стене здания. Притом влага, попадающая в трещины, при замерзании будет увеличиваться в размерах, и они также станут расти. Трещины могут образоваться и из-за отсутствия монолитных обвязочных поясов по периметру дома на уровне перекрытий, а также если не предусмотрено армирование под оконными проёмами».
Опирание стропил на стену из газобетонных блоков:1. Стропильная нога2. Металлический уголок3. Мауэрлат4. Гидроизоляция5. Армопояс6. Шпилька7. Слой эффективной теплоизоляции8. Газобетонный блок
Стены и перекрытия из газобетона
Принципиальная разница между кладкой из газобетонных блоков и кладкой из других каменных материалов (крупноформатного кирпича, пенобетонных блоков и др.) заключается в том, что стену из газобетона возводят с использованием специального клеевого раствора на цементно-песчаной основе, толщина которого – всего 1 -3 мм (для сравнения: размер шва в кирпичной кладке – 10-15 мм). Шов – это мостик холода в конструкции стены, поскольку обладает большей теплопроводностью, и чем он тоньше – тем меньше потери тепла.
Столь тонкий шов возможен благодаря тому, что ведущие производители выпускают блоки с очень точной геометрией. Соблюдать толщину шва во время кладки позволяет специальный инструмент – кельма. Клеевым составом фиксируют как горизонтальную, так и вертикальную часть блока. Швы следует заполнять клеем на всю глубину кладки.
Первый ряд блоков укладывают поверх отсечной гидроизоляции (чаще всего рулонной битумной или битумнополимерной). Важный момент: блоки первого ряда фиксируют к основанию с помощью обычного цементно-песчаного раствора.
Дело в том, что верхняя поверхность фундамента не бывает идеально ровной (плоской), а подобный раствор (толщиной не менее 20 мм) позволяет нивелировать незначительные перепады по высоте (их допустимая величина – не более 20 мм). Очень важно добиться ровности первого ряда кладки, поскольку от этого зависит ровность стен всего здания. Небольшие перепады между соседними блоками устраняют с применением рубанка и шлифовальной доски.
Читайте также: Дом из газобетона – плюсы строительства
Для устройства эркеров или криволинейных поверхностей можно либо использовать готовые дугообразные модули, предлагаемые многими изготовителями, либо подрезать углы стандартных блоков ножовками по газобетону, либо – в случае большого радиуса – закруглять кладку за счёт шва.
Ряд производителей рекомендует предусматривать армирующие элементы через каждые 4 ряда блоков для повышения прочности кладки. Армирование можно выполнять с помощью сетки из оцинкованной стали, например, толщиной 3 мм с ячейками 50 х 50 мм. Однако при этом толщина шва будет 5-8 мм, и он станет мостиком холода.
а, б) Блоки укладывают с помощью специального клея на цементно-песчаной основе. Клей наносят на горизонтальную и вертикальную поверхность блока, используя для этого особый инструмент – кельму в) Для распиливания блоков предусмотрены ножовка и угольник. г, д) Поскольку толщина клеевого шва – всего 1 -3 мм, нет возможности выравнивать кладку за счёт него. А значит, надо тщательно выровнять фундамент и первые ряды кладкие) Блоки легко пилятся, что позволяет получить элементы нужных размеров
Поэтому лучше армировать металлическими прутами диаметром 8-12 мм, уложенными в горизонтальные штрабы, которые проделаны в кладке (на расстоянии не менее 60 мм от боковых граней блоков). Штрабы затем заполняют клеевым раствором. Для блока толщиной 375 мм обычно требуется два арматурных прута. Вместе с тем другие производители газобетона утверждают, что армировать рядовые участки кладки из их блоков не нужно, поскольку сами блоки и предлагаемый для них клеевой раствор обладают высокой прочностью.
Но даже при использовании таких блоков необходимо предусмотреть армирование подоконными проёмами (в предпоследнем ряду блоков, притом длина арматуры должна быть больше проёма не менее чем на 50 см с каждой стороны), а также монолитный обвязочный пояс (связывающий несущие стены) на уровне межэтажных перекрытий. Обвязочный пояс обязательно должен быть замкнутым. Он может представлять собой арматурный каркас, залитый бетоном. Но можно его создать и с помощью U-образных газобетонных блоков, предлагаемых многими производителями.
Комментарий специалиста
«Монолитный железобетонный пояс по периметру здания, связывающий воедино наружные стены, обязателен в сейсмоопасных зонах. Его непременно следует предусматривать и при строительстве на сильно- или среднепучинистых грунтах. Если же грунты слабопучи- нистые или непучинистые, то можно отказаться от него и выполнить распределительный пояс в виде кирпичной кладки, что значительно удешевит, упростит и ускорит процесс сооружения здания. Обычно кирпичную кладку делают высотой в три ряда и затем опирают на неё плиту или балки перекрытия. Толщину кладки подбирают в том числе с учётом того, что по периметру её необходимо закрыть теплоизоляционной вставкой (например, из пенополистирола), чтобы избежать промерзания через стену. А в случае оконного проёма большого размера следует выполнить армирование блоков подоконного ряда с помощью прутов диаметром 10-12 мм (укладывая их в штрабы и заливая цементным раствором), чтобы распределить нагрузку от тяжёлого оконного блока и тем самым предотвратить появление трещин по углам проёма».
Внутрь такого блока укладывают арматуру и заливают её бетоном, притом оболочка из газобетона уменьшает теплопотери через этот пояс. В то же время инженеры-конструкторы напоминают, что необходимость армирования определяется только на основании расчёта нагрузок в соответствии с проектом здания. И некоторые строительные компании после проведения расчётов отказались от применения обвязочного пояса и армирования в подоконных зонах при сооружении малоэтажных загородных домов, полагая, что они неоправданно увеличивают стоимость и сроки возведения здания. Добавим, что для перевязки внешних стен и внутренних перегородок предусматривают анкерные пластины из нержавеющей стали.
Читайте также: Из какого материала лучше строить дом
Существуют разные технологии выполнения перекрытий в доме из газобетона. Наиболее надёжным решением, к тому же подходящим для здания любой геометрии, является устройство монолитной железобетонной плиты (её толщина, как правило, 160 мм).
Однако это самый дорогой и не лишённый недостатков вариант, в частности, придётся долго ждать, пока бетон наберёт прочность, соответственно время строительства увеличится. Не менее надёжным, но более экономичным и быстрым в исполнении решением можно считать сборные железобетонные плиты перекрытия. Это готовые конструкции, поднимаемые с помощью крана.
Их недостаток – стандартные форма и размеры, а значит, в случае сложной геометрии здания (например, с эркерами) или при небольшом расстоянии между плитами понадобится дополнять перекрытие монолитными участками. К тому же такое перекрытие будет потолще – 220 мм.
Обратите внимание: чтобы минимизировать промерзание через перекрытие, обязательно устанавливают слой теплоизоляции (чаще всего из пенополистирола) между плитой и стеновым блоком. Если есть необходимость уложить перекрытие вручную (без применения крана) и в сжатые сроки, тогда можно использовать сборно-монолитное перекрытие, предлагаемое некоторыми производителями газобетона.
В его основе – железобетонные балки, изготавливаемые на заказ, требуемой длины (до 7 м) и небольшого сечения. Их устанавливают с определённым шагом, а между ними (с опорой на них) укладывают Т-образные газобетонные блоки. Далее настилают арматурную сетку и заливают её стяжкой толщиной 40-50 мм. Несущая способность такого перекрытия – до 450 кг/м2. Общая толщина конструкции – порядка 240 мм. Добавим, что в большинстве случаев допустимо опирать перекрытие на газобетонную кладку, поверх которой нанесён цемент-но-песчаный раствор слоем около 50 мм. Реже всего применяют перекрытия по деревянным балкам.
При устройстве оконных и дверных проёмов предусматривают перемычки. Самый дешёвый и простой в исполнении вариант – металлические уголки (обязательно защищённые антикоррозийными составами), на которые опирают обычные блоки.
Также можно устанавливать перемычки из сборных или монолитных железобетонных балок (это самое надёжное решение, но чреватое мостиками холода, поэтому балки нужно закрывать снаружи теплоизоляцией), готовых армированных балок из газобетона, U-образных газобетонных блоков с заполнением арматурой и бетоном и др. Отметим, что U-образные блоки с таким заполнением и закладными анкерами обычно предусматривают и для верхнего ряда кладки, на которую будет опираться мауэрлат – опорный брус для стропильной системы.
Выбирая отделочный материал для фасада, стоит помнить, что газобетон обладает высокой паропроницаемостью, а значит, отделка не должна препятствовать выходу водяного пара из конструкции стены, чтобы исключить накопление влаги в зоне контакта стены и отделки. Так, допустимо применять минеральные штукатурки высокой прочности (возможны тонкослойные и толстослойные варианты их нанесения) с последующей окраской паропроницаемыми красками.
Отделка внешней стены тонкослойной штукатуркой:1. Газобетонный блок2. Грунтовочный слой3. Фасадная стеклосетка4. Декоративная штукатурка
В случае облицовки лицевым кирпичом следует оставлять вентилируемый зазор около 40 мм между газобетонной стеной и кирпичной кладкой для удаления водяного пара (самонесущую кирпичную стену соединяют с газобетонными блоками при помощи гибких связей). Несмотря на высокие теплотехнические характеристики газобетона, некоторые застройщики предпочитают дополнительно утеплять наружные стены.
Не рекомендуют использовать для этих целей теплоизоляцию с низкой паро-проницаемостью (например, пенополистирол). Лучше применять «дышащие» волокнистые плиты высокой плотности (как правило, 145-150 кг/м3).
Их фиксируют к стене минеральным клеем и тарельчатыми дюбелями, после чего оштукатуривают (в том числе с последующей окраской) паропроницаемыми составами. Или закрывают лицевым кирпичом с обязательным устройством вентзазора.
Читайте также: Веранда своими руками
Комментарий специалиста
Газобетонные блоки толщиной 375 мм, имеющие плотность D500, в сочетании со штукатурной отделкой отвечают требованиям по сопротивлению теплопередаче ограждающих конструкций, предъявляемым СНиП 23-02-2003 «Тепловая защита здания» для средней полосы России. Имеет ли смысл дополнительно утеплять дом из газобетона? Однозначного ответа на этот вопрос нет. Если заказчик с помощью теплоизоляции стремится свести к минимуму затраты на отопление коттеджа, то в этом есть смысл. Однако эффект будет незначительным, если не предусмотрены другие меры по сбережению тепла – качественное утепление крыши и перекрытий на границе с холодными зонами, энергоэффективные окна, теплоизолированные двери и пр. Иными словами, должна быть реализована концепция пассивного дома. Вместе с тем срок службы утеплителя будет значительно меньше, чем срок службы стеновых конструкций, и заказчик должен быть готов к тому, что через несколько десятков лет может понадобиться реконструировать фасад здания».
Автор: Известный строительный журналист А.Левенко. Фото В.Ковалев. Ytong
Реклама
Ниже другие записи по теме "Как сделать своими руками - домохозяину!"
Подпишитесь на обновления в наших группах.
Будем друзьями!
kak-svoimi-rukami.com
Адрес:
603034 Нижний НовгородЛенинский район ул. Ростовская
д.13 офис №2
Телефон:
(831) 216-17-138(987) 544-18-81
email:
[email protected]COPYRIGHT © 2018
Все права защищены